Rodney Brooks’ Three Laws of Robotics
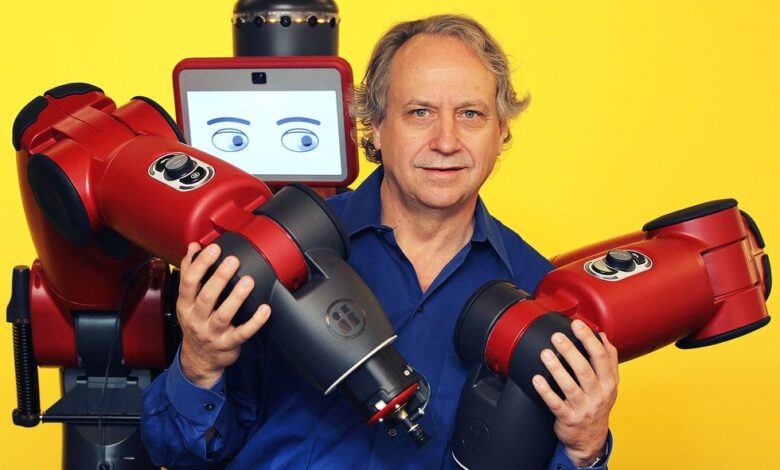
Rodney Brooks is the Panasonic Professor of Robotics (emeritus) at MIT, where he was director of the AI Lab and then CSAIL. He has been cofounder of iRobot, Rethink Robotics, and Robust AI, where he is currently CTO. This article is shared with permission from his blog.
Here are some of the things I’ve learned about robotics after working in the field for almost five decades. In honor of Isaac Asimov and Arthur C. Clarke, my two boyhood go-to science fiction writers, I’m calling them my three laws of robotics.
The visual appearance of a robot makes a promise about what it can do and how smart it is. It needs to deliver or slightly over deliver on that promise or it will not be accepted.
When robots and people coexist in the same spaces, the robots must not take away from people’s agency, particularly when the robots are failing, as inevitably they will at times.
Technologies for robots need 10+ years of steady improvement beyond lab demos of the target tasks to mature to low cost and to have their limitations characterized well enough that they can deliver 99.9 percent of the time. Every 10 more years gets another 9 in reliability.
Below I explain each of these laws in more detail. But in a related post here are my three laws of artificial intelligence.
Note that these laws are written from the point of view of making robots work in the real world, where people pay for them, and where people want return on their investment. This is very different from demonstrating robots or robot technologies in the laboratory.
In the lab there is phalanx of graduate students eager to demonstrate their latest idea, on which they have worked very hard, to show its plausibility. Their interest is in showing that a technique or technology that they have developed is plausible and promising. They will do everything in their power to nurse the robot through the demonstration to make that point, and they will eagerly explain everything about what they have developed and what could come next.
In the real world there is just the customer, or the employee or relative of the customer. The robot has to work with no external intervention from the people who designed and built it. It needs to be a good experience for the people around it or there will not be more sales to those, and perhaps other, customers.
So these laws are not about what might, or could, be done. They are about real robots deployed in the real world. The laws are not about research demonstrations. They are about robots in everyday life.
The Promise Given By Appearance
My various companies have produced all sorts of robots and sold them at scale. A lot of thought goes into the visual appearance of the robot when it is designed as that tells the buyer or user what to expect from it.
The iRobot Roomba was carefully designed to meld looks with function.iStock
The Roomba, from iRobot, looks like a flat disk. It cleans floors. The disk shape was so that it could turn in place without hitting anything it wasn’t already hitting. The low profile of the disk was so that it could get under the toe kicks in kitchens and clean the floor that is overhung just a little by kitchen cabinets. It does not look like it can go up and down stairs or even a single step up or step down in a house and it cannot. It has a handle, which make it look like it can be picked up by a person, and it can be. Unlike fictional Rosey the Robot it does not look like it could clean windows, and it cannot. It cleans floors, and that is it.
The Packbot, the remotely operable military robot, also from iRobot, looked very different indeed. It has tracked wheels, like a miniature tank, and that appearance promises anyone who looks at it that it can go over rough terrain, and is not going to be stopped by steps or rocks or drops in terrain. When the Fukushima disaster happened, in 2011, Packbots were able to operate in the reactor buildings that had been smashed and wrecked by the tsunami, open door handles under remote control, drive up rubble covered staircases and get their cameras pointed at analog pressure and temperature gauges so that workers trying to safely secure the nuclear plant had some data about what was happening in highly radioactive areas of the plant.
An iRobot PackBot picks up a demonstration object at the Joint Robotics Repair Detachment at Victory Base Complex, Baghdad, Iraq.Alamy
The point of this first law of robotics is to warn against making a robot appear more than it actually is. Perhaps that will get funding for your company leading investors to believe that in time the robot will be able to do all the things its physical appearance suggests it might be able to do. But it is going to disappoint customers when it cannot do the sorts of things that something with that physical appearance looks like it can do. Glamming up a robot risks overpromising what the robot as a product can actually do. That risks disappointing customers. And disappointed customers are not going to be an advocate for your product/robot, nor be repeat buyers.
Preserving People’s Agency
The worst thing for its acceptance by people that a robot can do in the workplace is to make their jobs or lives harder, by not letting them do what they need to do.
Robots that work in hospitals taking dirty sheets or dishes from a patient floor to where they are to be cleaned are meant to make the lives of the nurses easier. But often they do exactly the opposite. If the robots are not aware of what is happening and do not get out of the way when there is an emergency they will probably end up blocking some life saving work by the nurses—e.g., pushing a gurney with a critically ill patient on it to where they need to be for immediate treatment. That does not endear such a robot to the hospital staff. It has interfered with their main job function, a function of which the staff is proud, and what motivates them to do such work.
A lesser, but still unacceptable behavior of robots in hospitals, is to have them wait in front of elevator doors, central, and blocking for people. It makes it harder for people to do some things they need to do all the time in that environment—enter and exit elevators.
Those of us who live in San Francisco or Austin, Texas, have had first hand views of robots annoying people daily for the last few years. The robots in question have been autonomous vehicles, driving around the city with no human occupant. I see these robots every single time I leave my house, whether on foot or by car.
Some of the vehicles were notorious for blocking intersections, and there was absolutely nothing that other drivers, pedestrians, or police could do. We just had to wait until some remote operator hidden deep inside the company that deployed them decided to pay attention to the stuck vehicle and get it out of people’s way. Worse, they would wander in to the scene of a fire where there were fire trucks and fire fighters and actual buildings on fire, get confused and just stop, sometime on top of the fire hoses.
There was no way for the fire fighters to move the vehicles, nor communicate with them. This is in contrast to an automobile driven by a human driver. Fire fighters can use their normal social interactions to communicate with a driver, and use their privileged position in society as front line responders to apply social pressure on a human driver to cooperate with them. Not so with the autonomous vehicles.
The autonomous vehicles took agency from people going about their regular business on the streets, but worse took away agency from firefighters whose role is to protect other humans. Deployed robots that do not respect people and what they need to do will not get respect from people and the robots will end up undeployed.
Robust Robots That Work Every Time
Making robots that work reliably in the real world is hard. In fact, making anything that works physically in the real world, and is reliable, is very hard.
For a customer to be happy with a robot it must appear to work every time it tries a task, otherwise it will frustrate the user to the point that they will question whether it make their life better or now.
But what does appear mean here? It means that the user can have the assumption that it going to work, as their default understanding of what will happen the world.
The tricky part is that robots interact with the real physical world.
Software programs interact with a well understood abstracted machine, so they tend not fail in a manner where the instructions in them do not get executed in a consistent way by the hardware on which they are running. Those same programs may also interact with the physical world, be it a human being, a network connection, or an input device like a mouse. It is then that the programs might fail as the instructions in them are based on assumptions in the real world that are not met.
Robots are subject to forces in the real world, subject to the exact position of objects relative to them, and subject to interacting with humans who are very variable in their behavior. There are no teams of graduate students or junior engineers eager to make the robot succeed on the 8,354th attempt to do the same thing that has worked so many times before. Getting software that adequately adapts to the uncertain changes in the world in that particular instance and that particular instant of time is where the real challenge arises in robotics.
Great looking videos are just not the same things as working for a customer every time. Most of what we see in the news about robots is lab demonstrations. There is no data on how general the solution is, nor how many takes it took to get the video that is shown. Even worse sometimes the videos are tele-operated or sped up many times over.
I have rarely seen a new technology that is less than ten years out from a lab demo make it in to a deployed robot. It takes time to see how well the method works, and to characterize it well enough that it is unlikely to fail in a deployed robot that is working by itself in the real world. Even then there will be failures, and it takes many more years of shaking out the problem areas and building it into the robot product in a defensive way so that the failure does not happen again.
Most robot require kill buttons or estops on them so that a human can shut them down. If a customer ever feels the need to hit that button then the people who have built and sold the robot have failed. They have not made it operate well enough that the robot never gets into a state where things are going that wrong.
IEEE Spectrum