How Zipline Designed Its Droid Delivery System
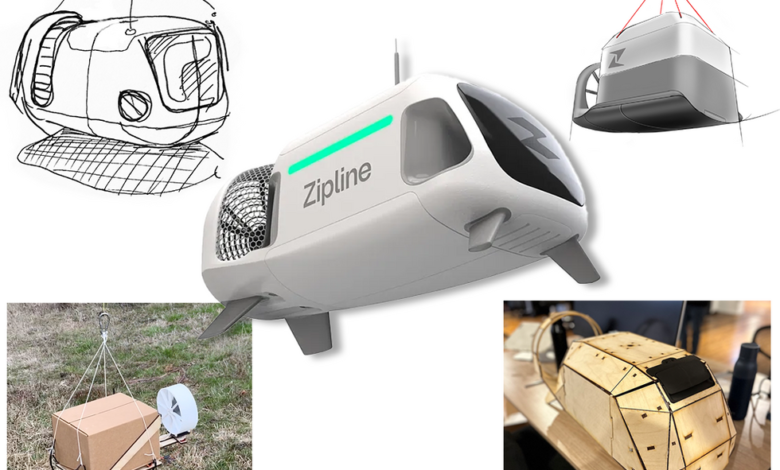
About a year ago, Zipline introduced Platform 2, an approach to precision urban drone delivery that combines a large hovering drone with a smaller package-delivery “Droid.” Lowered on a tether from the belly of its parent Zip drone, the Droid contains thrusters and sensors (plus a 2.5- to 3.5-kilogram payload) to reliably navigate itself to a delivery area of just one meter in diameter. The Zip, meanwhile, safely remains hundreds of meters up. After depositing its payload, the Droid rises back up to the drone on its tether, and off they go.
At first glance, the sensor and thruster-packed Droid seems complicated enough to be bordering on impractical, especially when you consider the relative simplicity of other drone delivery solutions, which commonly just drop the package itself on a tether from a hovering drone. I’ve been writing about robots long enough that I’m suspicious of robotic solutions that appear to be overengineered, since that’s always a huge temptation with robotics. Like, is this really the best way of solving a problem, or is it just the coolest way?
We know the folks at Zipline pretty well, though, and they’ve certainly made creative engineering work for them, as we saw when we visited one of their “nests” in rural Rwanda. So as Zipline nears the official launch of Platform 2, we spoke with Zipline cofounder and CTO Keenan Wyrobek, Platform 2 lead Zoltan Laszlo, and industrial designer Gregoire Vandenbussche to understand exactly why they think this is the best way of solving precision urban drone delivery.
First, a quick refresher. Here’s what the delivery sequence with the vertical takeoff and landing (VTOL) Zip and the Droid looks like:
The system has a service radius of about 16 kilometers (10 miles), and it can make deliveries to outdoor spaces of “any meaningful size.” Visual sensors on the Droid find the delivery site and check for obstacles on the way down, while the thrusters compensate for wind and movement of the parent drone. Since the big VTOL Zip remains well out of the way, deliveries are fast, safe, and quiet. But it takes two robots to pull off the delivery rather than just one.
On the other end is the infrastructure required to load and charge these drones. Zipline’s Platform 1 drones require a dedicated base with relatively large launch and recovery systems. With Platform 2, the drone drops the Droid into a large chute attached to the side of a building so that the Droid can be reloaded, after which it pulls the Droid out again and flies off to make the delivery:
“We think it’s the best delivery experience. Not the best drone delivery experience, the best delivery experience,” Zipline’s Wyrobek tells us. That may be true, but the experience also has to be practical and sustainable for Zipline to be successful, so we asked the Zipline team to explain the company’s approach to precision urban delivery.
Zipline on:
Approach to drone deliveryConcept for Droid designDesigning for cutenessMaking pinpoint deliveries
IEEE Spectrum: What problems is Platform 2 solving, and why is it necessary to solve those problems in this specific way?
Keenan Wyrobek: There are literally billions of last-mile deliveries happening every year in [the United States] alone, and our customers have been asking for years for something that can deliver to their homes. With our long-range platform, Platform 1, we can float a package down into your yard on a parachute, but that takes some space. And so one half of the big design challenge was how to get our deliveries precise enough, while the other half was to develop a system that will bolt on to existing facilities, which Platform 1 doesn’t do.
Zoltan Laszlo: Platform 1 can deliver within an area of about two parking spaces. As we started to actually look at the data in urban areas using publicly available lidar surveys, we found that two parking spaces serves a bit more than half the market. We want to be a universal delivery service.
But with a delivery area of 1 meter in diameter, which is what we’re actually hitting in our delivery demonstrations for Platform 2, that gets us into the high 90s for the percentage of people that we can deliver to.
Wyrobek: When we say “urban,” what we’re talking about is three-story sprawl, which is common in many large cities around the world. And we wanted to make sure that our deliveries could be precise enough for places like that.
There are some existing solutions for precision aerial delivery that have been operating at scale with some success, typically by winching packages to the ground from a VTOL drone. Why develop your own technique rather than just going with something that has already been shown to work?
Laszlo: Winching down is the natural extension of being able to hover in place, and when we first started, we were like, “Okay, we’re just going to winch down. This will be great, super easy.”
So we went to our test site in Half Moon Bay [on the Northern California coast] and built a quick prototype of a winch system. But as soon as we lowered a box down on the winch, the wind started blowing it all over the place. And this was from the height of our lift, which is less than 10 meters up. We weren’t even able to stay inside two parking spaces, which told us that something was broken with our approach.
The aircraft can sense the wind, so we thought we’d be able to find the right angle for the delivery and things like that. But the wind where the aircraft is may be different from the wind nearer the ground. We realized that unless we’re delivering to an open field, a package that does not have active wind compensation is going to be very hard to control. We’re targeting high-90th percentile in terms of availability due to weather—even if it’s a pretty blustery day, we still want to be able to deliver.
Wyrobek: This was a wild insight when we really understood that unless it’s a perfect day, using a winch actually takes almost as much space as we use for Platform 1 floating a package down on a parachute.
Engineering test footage of Zipline’s Platform 2 docking system at their test site in Half Moon Bay in California.
How did you arrive at this particular delivery solution for Platform 2?
Laszlo: I don’t remember whose idea it was, but we were playing with a bunch of different options. Putting thrusters on the tether wasn’t even the craziest idea. We had our Platform 1 aircraft, which was reliable, so we started with looking at ways to just make that aircraft deliver more precisely. There was only so much more we could do with passive parachutes, but what does an active, steerable parachute look like? There are remote-controlled paragliding toys out there that we tested, with mixed results—the challenge is to minimize the smarts in your parachute, because there’s a chance you won’t get it back. So then we started some crazy brainstorming about how to reliably retrieve the parachute.
Wyrobek: One idea was that the parachute would come with a self-return envelope that you could stick in the mail. Another idea was that the parachute would be steered by a little drone, and when the package got dropped off, the drone would reel the parachute in and then fly back up into the Zip.
Laszlo: But when we realized that the package has to be able to steer itself, that meant the Zip doesn’t need to be active. The Zip doesn’t need to drive the package, it doesn’t even need to see the package, it just needs to be a point up in the sky that’s holding the package. That let us move from having the Zip 50 feet up, to having it 300 feet up, which is important because it’s a big, heavy drone that we don’t want in our customer’s space. And the final step was adding enough smarts to the thing coming down into your space to figure out where exactly to deliver to, and of course to handle the wind.
Once you knew what you needed to do, how did you get to the actual design of the droid?
Gregoire Vandenbussche: Zipline showed me pretty early on that they were ready to try crazy ideas, and from my experience, that’s extremely rare. When the idea of having this controllable tether with a package attached to it came up, one of my first thoughts was that from a user standpoint, nothing like this exists. And the difficulty of designing something that doesn’t exist is that people will try to identify it according to what they know. So we had to find a way to drive that thinking towards something positive.
Early Droid concept sketches by designer Gregoire Vandenbussche featured legs that would fold up after delivery.Zipline
First we thought about putting words onto it, like “hello” or something, but the reality is that we’re an international company and we need to be able to work everywhere. But there’s one thing that’s common to everyone, and that’s emotions—people are able to recognize certain things as being approachable and adorable, so going in that direction felt like the right thing to do. However, being able to design a robot that gives you that kind of emotion but also flies was quite a challenge. We took inspiration from other things that move in 3D, like sea mammals—things that people will recognize even without thinking about it.
Vandenbussche’s sketches show how the design of the Droid was partially inspired by dolphins.Zipline
Now that you say it, I can definitely see the sea mammal inspiration in the drone.
Vandenbussche: There are two aspects of sea mammals that work really well for our purpose. One of them is simplicity of shape; sea mammals don’t have all that many details. Also, they tend to be optimized for performance. Ultimately, we need that, because we need to be able to fly. And we need to be able to convey to people that the drone is under control. So having something you can tell is moving forward or turning or moving away was very helpful.
Wyrobek: One other insight that we had is that Platform 2 needs to be small to fit into tight delivery spaces, and it needs to feel small when it comes into your personal space, but it also has to be big enough inside to be a useful delivery platform. We tried to leverage the chubby but cute look that baby seals have going on.
The design journey was pretty fun. Gregoire would spend two or three days coming up with a hundred different concept sketches. We’d do a bunch of brainstorming, and then Gregoire would come up with a whole bunch of new directions, and we’d keep exploring. To be clear, no one would describe our functional prototypes from back then as “cute.” But through all this iteration eventually we ended up in an awesome place.
And how do you find that place? When do you know that your robot is just cute enough?
One iteration of the Droid, Vandenbussche determined, looked too technical and intimidating.Zipline
Vandenbussche: It’s finding the balance around what’s realistic and functional. I like to think of industrial design as taking all of the constraints and kind of playing Tetris with them until you get a result that ideally satisfies everybody. I remember at one point looking at where we were, and feeling like we were focusing too much on performance and missing that emotional level. So, we went back a little bit to say, where can we bring this back from looking like a highly technical machine to something that can give you a feeling of approachability?
Laszlo: We spent a fair bit of time on the controls and behaviors of the droid to make sure that it moves in a very approachable and predictable way, so that you know where it’s going ahead of time and it doesn’t behave in unexpected ways. That’s pretty important for how people perceive it.
We did a lot of work on how the droid would descend and approach the delivery site. One concept had the droid start to lower down well before the Zip was hovering directly overhead. We had simulations and renderings, and it looked great. We could do the whole delivery in barely over 20 seconds. But even if the package is far away from you, it still looks scary because [the Zip is] moving faster than you would expect, and you can’t tell exactly where it’s going to deliver. So we deleted all that code, and now it just comes straight down, and people don’t back away from the Droid anymore. They’re just like, “Oh, okay, cool.”
How did you design the thrusters to enable these pinpoint deliveries?
Early tests of the Droid centered around a two-fan version.Zipline
Laszlo: With the thrusters, we knew we wanted to maximize the size of at least one of the fans, because we were almost always going to have to deal with wind. We’re trying to be as quiet as we can, so the key there is to maximize the area of the propeller. Our leading early design was just a box with two fans on it:
Two fans with unobstructed flow meant that it moved great, but the challenge of fitting it inside another aircraft was going to be painful. And it looked big, even though it wasn’t actually that big.
Vandenbussche: It was also pretty intimidating when you had those two fans facing you and the Droid coming toward you.
A single steerable fan [left] that acted like a rudder was simpler in some ways, but as the fan got larger, the gyroscopic effects became hard to manage. Instead of one steerable fan, how about two steerable fans? [right] Omnidirectional motion was possible with this setup, but packaging it inside of a Zip didn’t work.Zipline
Laszlo: We then started looking at configurations with a main fan and a second smaller fan, with the bigger fan at the back pushing forward and the smaller fan at the front providing thrust for turning. The third fan we added relatively late because we didn’t want to add it at all. But we found that [with two fans] the droid would have to spin relatively quickly to align to shifting winds, whereas with a third fan we can just push sideways in the direction that we need.
What kind of intelligence does the Droid have?
The current design of Zipline’s Platform 2 Droid is built around a large thruster in the rear and two smaller thrusters at the front and back.Zipline
Wyrobek: The Droid has its own little autopilot, and there’s a very simple communications system between the two vehicles. You may think that it’s a really complex coordinated control problem, but it’s not: The Zip just kind of hangs out, and the Droid takes care of the delivery. The sensing challenge is for the Droid to find trees and powerlines and things like that, and then find a good delivery site.
Was there ever a point at which you were concerned that the size and weight and complexity would not be worth it?
Wyrobek: Our mindset was to fail fast, to try things and do what we needed to do to convince ourselves that it wasn’t a good path. What’s fun about this kind of iterative process is oftentimes, you try things and you realize that actually, this is better than we thought.
Laszlo: We first thought about the Droid as a little bit of a tax, in that it’s costing us extra weight. But if your main drone can stay high enough up that it avoids trees and buildings, then it can just float around up there. If it gets pushed around by the wind, it doesn’t matter because the Droid can compensate.
Wyrobek: Keeping the Zip at altitude is a big win in many ways. It doesn’t have to spend energy station-keeping, descending, and then ascending again. We just do that with the much smaller Droid, which also makes the hovering phase much shorter. It’s also much more efficient to control the small droid than the large Zip. And having all of the sensors on the Droid very close to the area that you’re delivering to makes that problem easier as well. It may look like a more complex system from the outside, but from the inside, it’s basically making all the hardest problems much easier.
Over the past year, Zipline has set up a bunch of partnerships to make residential deliveries to consumers using Droid starting in 2024, including prescriptions from Cleveland Clinic in Ohio, medical products from WellSpan Health in Pennsylvania, tasty food from Mendocino Farms in California, and a little bit of everything from Walmart starting in Dallas. Zipline’s plan is to kick things off with Platform 2 later this year.
IEEE Spectrum