Inkjets Are for More Than Just Printing
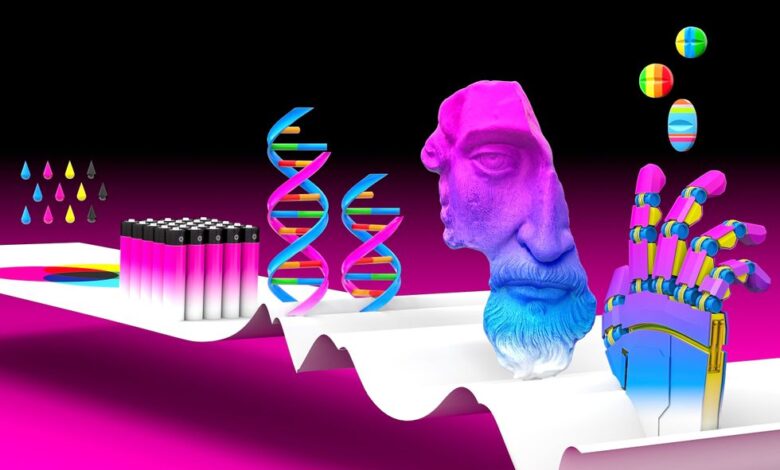
In the early 1980s, offices were noisy places, filled with the sound of metal striking inked ribbons to mark characters on paper. IBM Selectric typewriters clacked, daisy wheel printers clattered, and dot-matrix printers made loud ripping sounds.
Today, those noises are gone. And though we do spend more time reading on screens, we haven’t stopped printing on paper.
The main reason for the quiet? The inkjet printer. While laser printers do the big printing jobs in commercial settings, the inkjet printer has become
the printer most of us use at home and at the office.
The printhead of an inkjet printer performs a remarkable task. Even at the coarse resolution of 96 dots per inch (dpi), as was typical for the first models in the 1980s, the distance from dot center to dot center is a mere 260 micrometers. To fill a standard letter page that has 2.5-centimeter margins would require more than half a million individual ink droplets. Delivery of those tiny droplets involves moving them with very precise control, repeated a vast number of times as rapidly as possible. This process is ideally suited for microelectromechanical systems (MEMS), which are electronic devices with microscopic components that employ movement.
If there is a way to package something in microscopic droplets with the appropriate fluid properties, chances are someone is looking to adapt inkjet technology to work with it.
As with all microtechnology, the specs of inkjet systems have evolved considerably over time. A typical inkjet printhead in the mid-1980s had 12 nozzles working in parallel, each one emitting up to 1,350 droplets per second, to print 150 alphanumeric characters per second. Today, a high-end inkjet printhead used in a commercial printing press may contain 21,000 nozzles, each nozzle printing 20,000 to 150,000 dots per second. Each drop of ink may be just 1.5 picoliters—a picoliter is one-trillionth of a liter—and measure roughly 14 micrometers in diameter.
Surpassing the visions of its creators, the inkjet technology used in these printers has found a host of applications beyond putting dots on paper. These include making DNA microarrays for genomics, creating electrical traces for printed circuit boards, and building 3D-printed structures. Future uses could include personalized medicine and development of advanced batteries.
Indeed, a search for patents containing the word “inkjet” today returns more than 92,000 results. If there is a way to package something in microscopic droplets with the appropriate fluid properties, chances are someone is looking to adapt inkjet technology to work with it.
How MEMS Transformed Inkjet Printing
Inkjet technology dates back to 1948, when Swedish inventor
Rune Elmqvist patented a chart recorder wherein a very thin glass tube emitting a continuous jet of ink was steered to make a trace on a moving strip of paper. A couple of years later, he demonstrated his invention in the form of a device for recording electrocardiograms.
In 1965, Richard G. Sweet of Stanford University
developed a chart recorder in which the jet of ink was broken into a uniform stream of electrically charged droplets. Diverter electrodes on either side of the stream could permit the drops to proceed straight to the paper, or else deflect them onto an absorbent pad or into a gutter to be collected and reused.
In April 1984, the HP ThinkJet [top] ushered in the era of desktop inkjet printing. The Thinkjet’s ink cartridge [bottom] delivered thousands of microscopic droplets a second from 12 nozzles. The MEMS technology to perform that feat was entirely within the printhead.HP
This technology is called continuous inkjet printing, and by 1976 IBM had incorporated it in a commercial printer, the
IBM 6640. But continuous inkjets lose ink to evaporation even when recycling is used, limiting their appeal.
To get around the wastefulness of continuous inkjets, others worked on developing drop-on-demand inkjet printers, where each orifice on the printhead emits one drop of ink at a time, avoiding the waste of a continual flow of drops. Surface tension holds the ink in place in a tiny open nozzle until a mechanism pushes the ink to eject a drop. Each drop hitting the paper creates a dot, and moving the printhead back and forth builds up an image. A printhead with multiple orifices can emit many drops of ink simultaneously, so each pass of the printhead across the page adds a strip of the image, not just a single drop-thin line.
In the late 1970s, Siemens was the first to sell a drop-on-demand inkjet printer. It came not as a stand-alone device like a modern desktop printer, but as an integral part of a computer terminal, the
Siemens PT80i (Printer Terminal 80 Inkjet). The printer used piezoelectric actuators surrounding 12 ink tubes, which fed 12 nozzles to shoot ink droplets, printing 270 characters per second.
Piezoelectric devices rely on how some materials, such as ceramic lead-zirconate-titanate (PZT), change shape when subjected to a voltage. This effect has proved extremely useful in MEMS in general, for generating precise forces and motion on command. If a layer of PZT is bonded to a nonpiezoelectric material, forming what’s called a bimorph, it will bend when exposed to a voltage. In the piezoelectric inkjet nozzle, the bending of the bimorph pushes ink out of the orifice. [For another application of piezoelectric MEMS technology, see “How Ultrasound Became Ultra Small.”]
The HP Jet Fusion 5200 industrial 3D printer uses an inkjet process to build parts out of nylon, polypropylene, or polyurethane.HP
This novel printing technology, however, was not yet as dependable as proven impact printers in the 1970s, and the whole Siemens terminal became unusable if the printer failed, so it didn’t catch on.
Meanwhile, researchers at both Hewlett-Packard and Canon noticed that ink would boil and splatter when exposed to a hot element like a soldering iron, and they decided to turn that splattering into a useful inkjet printing mechanism. They knew that a resistor could be used as a heating element and could be miniaturized with the same technology as that used for integrated circuits. In the printers they built, each ink nozzle contains a resistor instead of a piezoelectric actuator. An electrical pulse heats the resistor, which flash-boils a thin layer of the ink, forming a rapidly expanding vapor bubble that pushes a droplet of ink out through the orifice.
This work led to two competing versions of thermal inkjet technology coming to market at nearly the same time 40 years ago. (The same year, 1984, Epson introduced a stand-alone
piezoelectric inkjet printer.)
Hewlett-Packard’s
HP ThinkJet was its first desktop inkjet printer based on its thermal technology, and it was designed to connect to a personal computer for everyday printing. It had an immediate advantage over the recently developed laser printers: It was much cheaper. A desktop laser printer from HP cost US $3,500 (about $10,500 today); HP’s 2225A ThinkJet cost only $495 ($1,500 today). Inkjet printers also used far less power than laser printers did and were quieter. Admittedly, inkjets didn’t have great resolution—96 dpi compared with 300 for laser printers in those early days—and they were slow.
But the advantages outweighed the disadvantages (more so as the technology improved), and inkjet printers came to dominate the desktop and home printer markets. Today, more than 20 companies make inkjet printers, generating a market of
more than $100 billion annually and continuing to grow at more than 8 percent per year.
Printing DNA Microarrays With Inkjets
While the business of making inkjet printers matured and grew, some companies began exploring what other kinds of “ink” might be delivered with an inkjet. One of these was Agilent Technologies, a spin-off of Hewlett Packard with a focus on life-science and chemical-analysis technologies. Agilent developed a way to print strands of DNA from the four nucleic acid bases—cytosine (C), guanine (G), adenine (A), and thymine (T). Specifically, the company adapted existing DNA chemistries plus inkjet printing techniques to build
microarrays of DNA on glass slides for genomics work, such as measuring which genes are being expressed in an organism under various conditions. Academic researchers have shared open-source methods for converting existing inkjet printers to build their own microarrays, albeit with specs that are much more modest than the commercial systems.
A DNA microarray consists of a substrate, usually glass, with an array of small regions called spots where DNA strands are attached. Agilent produces arrays with as many as a million spots on a single 2.5-by-7.6-cm slide. An open-source system puts up to 10,000 in a somewhat smaller area. Each DNA strand is made of sequences of the bases C, G, A, and T. In double-stranded DNA, the strands have complementary sequences, which join up like rungs of a ladder, C joining with G, and A with T.
In the resting state [top] of an inkjet nozzle, the ink is held in place by surface tension. In a thermal inkjet nozzle [left], a voltage pulse to the heating resistor flash-vaporizes a thin layer of ink, producing an expanding vapor bubble [left, middle] that pushes a droplet of ink out through the orifice [left, bottom]. In less than a millisecond the vapor recondenses and the chamber cools and refills with ink, returning the nozzle to the resting state. A piezoelectric inkjet nozzle [right] is driven by a piezoelectric bimorph, which bends when a voltage is applied [right, middle] to push out an ink droplet [right, bottom].
A DNA microarray uses single-stranded DNA, and each spot has millions of strands with a common sequence. When a sample with copies of the complementary strand washes over the spot, those strands bind together with the strands anchored in the spot. The sample strands are tagged with fluorescent molecules, and the user learns which DNA sequences were present in the sample by examining which spots light up.
In Agilent’s method for fabricating a microarray, the printer makes multiple passes over the substrate, each pass adding one base to each strand in the spots, with intermediate steps to prepare for the next pass.
Adding a base is actually a three-step process. Each of the growing strands in the microarray spots has a molecular “cap” at the end that prevents the indiscriminate addition of more bases. So the first step is to remove or deactivate those caps by washing a solution over the nascent microarray. The second step is analogous to printing a page: At each spot on the microarray, the inkjet adds a dot of liquid containing the next monomer molecule (modified versions of C, G, A, or T) to be added to the end of the strand. These monomers each include a new cap so that only one molecule gets added to each strand. Although the newly added monomers are now attached to the strands, the connection is not fully stable, and so the third step applies an oxidizer solution that modifies the bonds, fully integrating the new monomers into the DNA structure. Rinse and repeat.
The versatility of the open-source inkjet construction allows researchers to rapidly build prototype arrays with whatever sequences they want to try out. A new array can be designed, synthesized, and used to analyze DNA in a single day.
One group reported a cycle time of 10 to 20 minutes to attach each base with their system, or about 13 hours to produce a batch of arrays, each with about 10,000 spots containing 40-base strands. For comparison’s sake, Agilent’s commercial microarrays typically have strands up to 60 bases long.
Agilent also uses its inkjet system to synthesize another genomic workhorse known as an
oligonucleotide library. The process is the same as for making a microarray, but at the end all the strands are cleaved from the substrate, dried, and packaged together in a single tube for the customer. Agilent’s inkjet-printed libraries have strands up to about 230 bases long.
3D Printing Using Two Inkjet Inks
Invent Medical—a Czech Republic startup partnered with HP—custom printed this helmet for correcting head-shape deformities [top]. An HP Jet Fusion 5200 printed this lipstick holder [bottom].Top: Invent Medical/HP; bottom: YOO Makeup/HP
In addition to printing two-dimensional pages and building one-dimensional molecular strands, inkjet technology has for many years been used to produce three-dimensional objects. One approach is a variant of powder-bed 3D printing, in which objects are built up by fusing or binding layers of powder in the desired pattern. The inkjet printhead applies droplets of a liquid binding agent to each layer of powder in the regions that will form the finished 3D items.
The HP Multi Jet Fusion (MJF) line of 3D printers extends this approach by depositing two types of ink: One is a binding promoter and the other a detailing agent, which is applied at the edges of the pattern to prevent the promoter from bleeding into the surrounding powder. A printhead carrying a wide array of inkjet nozzles dispenses these inks, and the array is quickly followed by a lighting bar to heat the powder, fusing it in the regions where the binding promoter is present. A fresh layer of powder is then spread over the entire printing area in readiness for the next cycle of the process. At the end, compressed air and a vacuum hose remove the unfused powder to reveal the completed 3D objects. The HP MJF printers perform this in a volume of up to 38 by 28 by 38 cm.
This model of a handheld vacuum cleaner with colored, translucent, and transparent parts was printed in one piece on a Mimaki inkjet 3D printer.Mimaki Engineering Co.
A quite different approach has been taken by
Mimaki Engineering Co. of Japan, which has introduced 3D printers with piezoelectric inkjet heads that dispense droplets of resin. The resins are photopolymers that are cured by ultraviolet light-emitting diodes after each layer is printed. Instead of using a powder bed that fills the entire build area, the printer deposits the resins on top of the growing structure. To deal with steep overhangs—such as an outstretched arm of a figurine—one of the resins produces a water-soluble material, which is used to build supports where needed. After the build is finished, these supports can be dissolved away.
Seven other resins provide colors that can include CMYK—the familiar cyan, magenta, yellow, and black inks of consumer inkjet printers—as well as white and clear, for a total of 10 million color combinations, comparable to the color depth that the human eye can discriminate. The resulting parts can combine solid color, colored transparency and translucency, and colorless transparency.
The printer provides a volume for building that measures 51 by 51 by 30 cm. Unlike with a powder-bed machine, small test parts can be made without filling the entire volume. In general, however, the Mimaki approach is slower than that of the HP MJF because it uses smaller printheads instead of a wide one that can cross the entire area in one sweep.
Inkjet’s Future
Inkjet printing’s strength is the ability to pattern various inks over large areas in short, rapid production runs at a reasonable cost. It cannot generally compete with standard high-volume production approaches, because those will usually be cheaper. Thus, a car enthusiast, for instance, may embrace 3D inkjet printing to make bespoke parts for repairs or other tinkering, but a high-volume car-parts manufacturer is not going to introduce such printers to its factory lines. Similarly, a company may build individual figurines from a customer’s design, printed by 3D inkjet, but the same technique won’t be economical for mass-producing models of the latest superhero. With many potential applications, it isn’t clear if there is a niche where the inkjet approach will win.
An example is the use of 3D inkjet printing for
personalized medicine. The idea is to produce tablets of a medication customized for a specific patient. Such personalized pills can include simple fine-tuning of the dose for an individual, as well as adjustments to the drug’s release rate—from very rapid to slow and sustained—through modifications to the binding agents and structure of the tablet. Rather than juggling multiple medications on a complicated schedule each day, a patient could take a single daily polypill—a 3D-printed tablet containing multiple medications, each with a different rate of release.
Researchers are exploring how to adapt existing 3D printing techniques, including inkjet, to make these personalized medications. Inkjet systems are particularly suited for printing drugs in the form of thin films, such as transdermal patches to be applied to the skin and buccal films to be held in the cheek, where drugs can pass directly to the bloodstream without first going through the digestive system.
A DNA microarray can be fabricated using an inkjet system to build custom-designed strands of DNA at each spot of the array. The printhead delivers a droplet of “ink” [left] containing modified monomers of one nucleotide [G, C, A, or T] to each spot. On the first print cycle, these monomers attach to the chemically treated glass surface. On subsequent print runs [right], a single monomer joins on the end of each growing DNA strand. Each monomer includes a protective cap to prevent other monomers from joining. Additional processes [not depicted here] wash away the nucleotide ink, apply a catalyst to complete the monomer bonding, and strip away the protective caps in preparation for the next printing step.Chris Philpot
These printed personalized medicines, however, would be expensive compared to fixed doses rolling off standard high-volume production lines. Thus the technique is likely to be reserved for relatively rare conditions.
Another potential application of 3D inkjet printing is in the fabrication of advanced lithium-ion batteries. The charging and discharging of these batteries relies on lithium ions moving from the battery’s electrodes to its electrolyte and back again, in the process releasing or absorbing electrons that produce the current flow. The energy-storage density of the standard electrode design can be increased by using thicker electrodes, but this compromises the power density—the rate of energy release—because a smaller proportion of the electrode is in close contact with the electrolyte.
A 3D inkjet could build electrodes with a detailed microstructure that allows the electrolyte to penetrate throughout the electrode volume. This could boost the ability of the active lithium ions and electrons to reach the entire electrode efficiently even when the electrode is larger, thereby increasing the energy storage and power density in tandem. For this vision to become a reality, however, researchers will need to learn more about how to formulate the “inks” for printing these electrodes: What are the best particle sizes and solvents to make an ink with fluid properties suitable for use in an inkjet system and that will produce stable printed structures with good electrochemical properties?
We think it is unlikely, however, that inkjet printing could compete with high-volume manufacturing on price. Inkjet printing of prototypes, on the other hand, may uncover an optimal battery design that can then be adapted for production by conventional techniques.
Inkjet systems have been demonstrated for a wide variety of applications beyond what we have discussed above:
Living cells can be printed, for instance, to form tissue structures for in vitro experiments. MEMS such as microscopic motors have been printed using inks containing nanoparticles of gold and silver as conductors and resin-based inks to act as insulators. Flexible sensors for health care monitoring have been printed using an electrically conducting polymer that responds to temperature differentials. And then there are all the ways inkjets are used to create images on media other than office printouts, such as printing of textiles, inkjet robots to apply custom automotive paint jobs, and the “Giclée” printing of fine art using archival-quality inks and substrates.
Each of these applications is like a colored dot on the vast canvas of human technology and activity. And while the dots from inkjets, powered by MEMS, may be only a single color among many others on that metaphorical page, the picture would be very different without them.
IEEE Spectrum